- Johs. Pedersen a/s
- 3D centre
3D technology
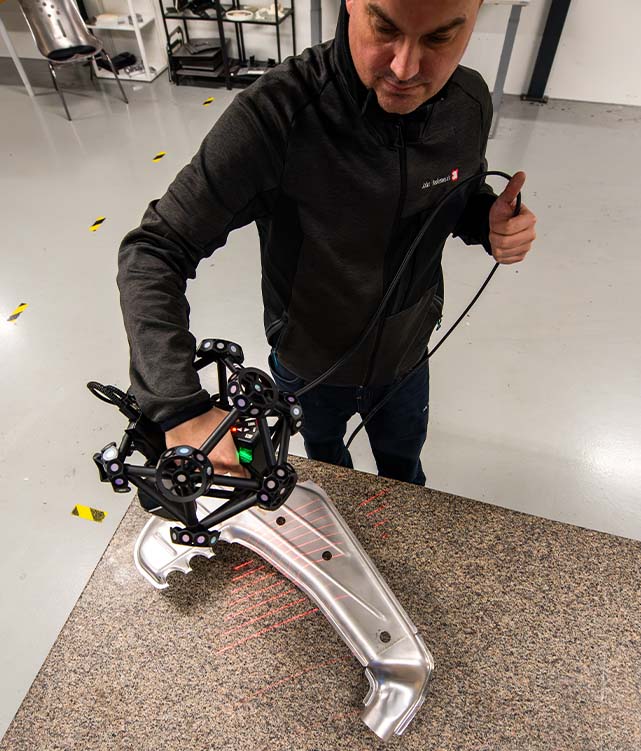
At Johs. Pedersen a/s, we can recreate old and obsolete spare parts using advanced 3D scanning and printing equipment.
Using 3D technology, we can produce tools in a faster and more economical manner than the traditional method of tool production.
3D scanning is a technology that can create a digital 3D model of a physical object. One of several technologies involves projecting a laser pattern onto the object, which is then captured by multiple sensors. The entire surface of the object is captured, not just individual points. The surface is optimized in accompanying modelling software. Any physical imperfections on the object are digitally removed, and holes can be resized or deleted. The object is saved in the desired file type, either as a “mesh” or a solid.
Our investment in 3D technology has enabled us to combine old existing manufacturing processes with new precise, flexible, and faster ways of producing tools. All of this results in more OEM-quality spare parts in a quicker and more affordable manner. The impossible solutions suddenly become realistic.
3D scans / prints
In principle, you can 3D-print anything that can be designed in a 3D modelling program. The benefits include flexibility and short production time. It is possible to print using various technologies and in an increasing variety of materials, including both plastic and metal.
During the manufacturing of items, 3D printing can be used to verify important details on an object, both on the finished product and throughout the process. Additionally, in certain cases, 3D printing replaces conventional machining of an item in a pressing, stamping, or welding tool. A 3D-scanned item can be printed directly but will, in most cases, first go through a drawing process.
3D print and scan
Shorter production time
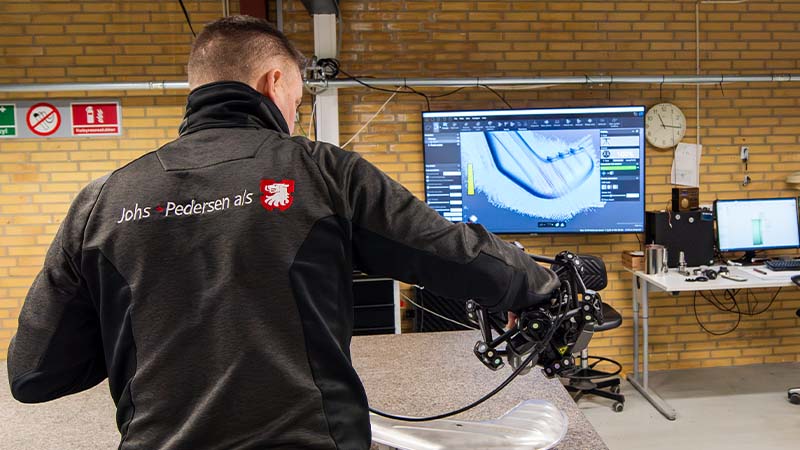
3D print and scan
Plastic and metal
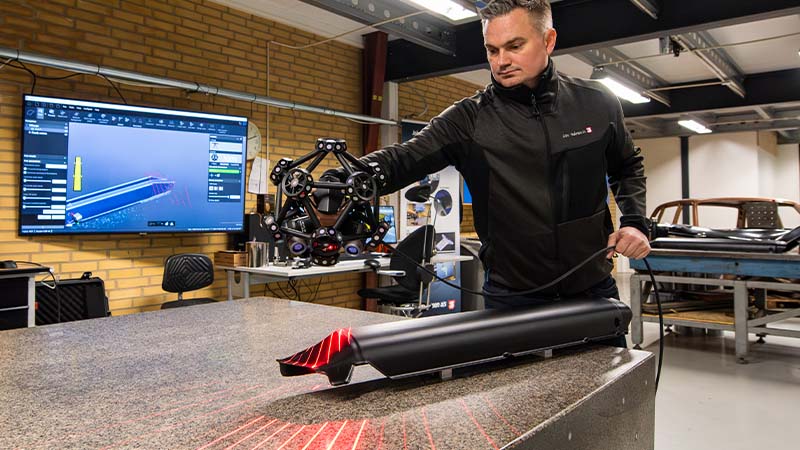
3D print and scan
Flexibility
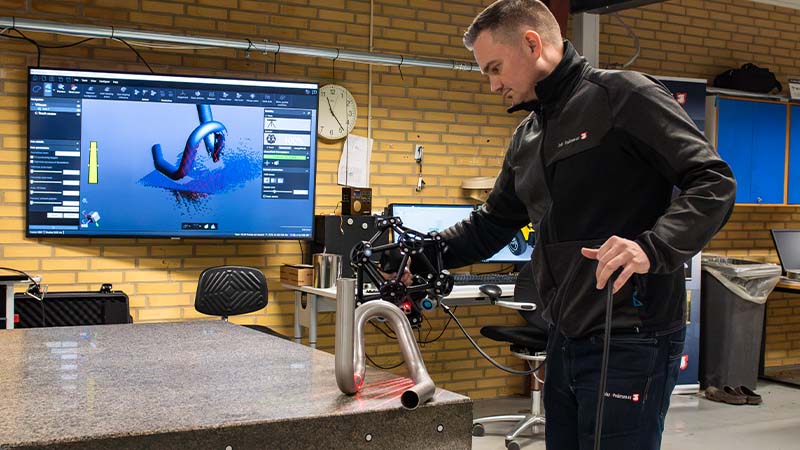
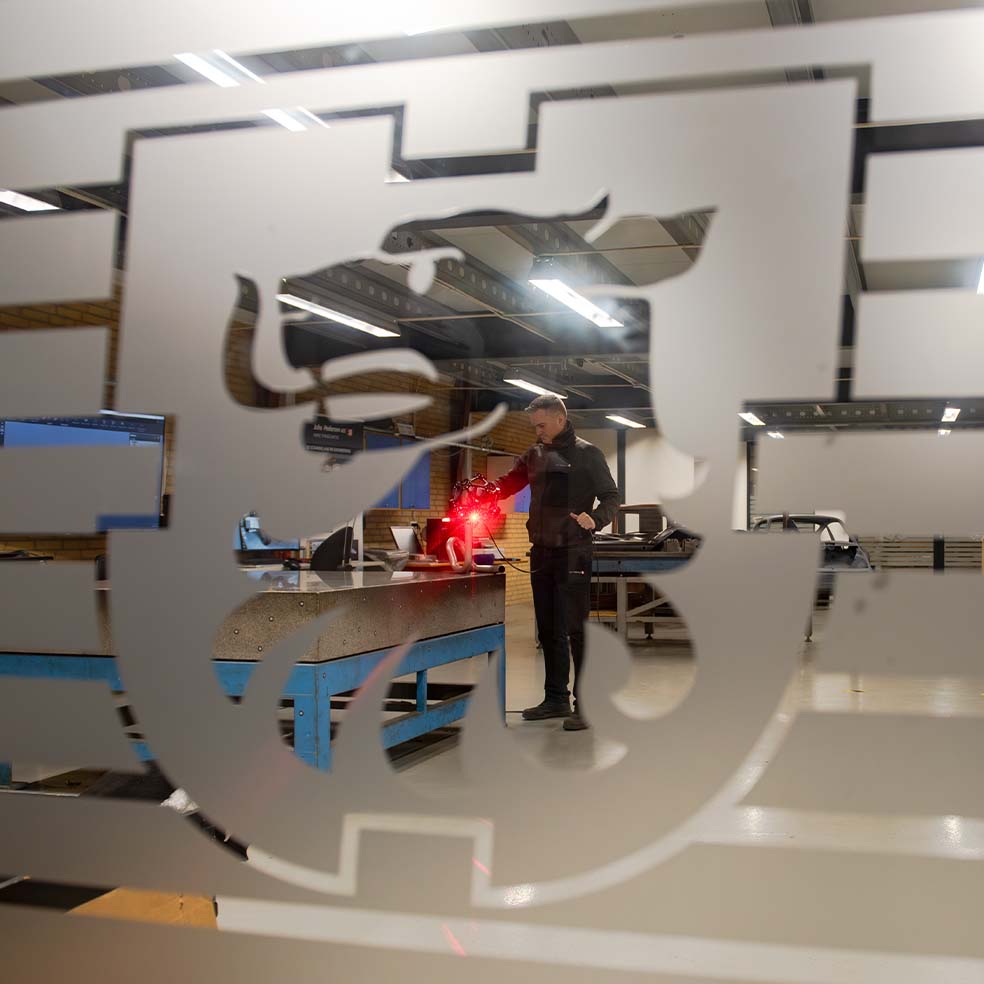
Prototypes for test and analysis
We leverage the results of 3D scanning and printing to create press molds that fit into our next production phase. This approach serves as a serious alternative to traditional CNC milling, which will reduce our tooling investments and increase our market accessibility. Furthermore, using 3D-scanned data, we can produce accurate prototypes for testing and analysis, accelerating our production process. At the same time, our investment in 3D technology allows us to combine old production methods with new ones, resulting in more OEM-quality spare parts in a faster and more economical manner.